基板ひずみ量評価
生産工程では、取扱いや加工方法によっては、基板にたわみストレスが加わることがあります。そこでは基板上に実装されたコンデンサにもたわみ ストレスが加わり、外部電極を起点にクラックが発生することがあります。コンデンサ内部にクラックが進みますと、たとえ初期の電気特性に問題がない場合でも、部品寿命が著しく低下することがあります。
したがって、工程における基板のたわみストレスが、できるだけ小さくなるような基板設計、工程設計を行ってください。
ひずみ量評価
- ・ひずみ量評価の必要性
基板にたわみストレスが加わりますと、変形した基板の凸側面は表面が伸びる方向に変形が生じます。この伸びが、引張り方向のひずみ量となります。ランド、はんだ、外部電極を通して、チップ底面側に引張り応力が発生し、引張り応力が外部電極端部に集中することで、脆性材料であるセラミック部分にクラックが発生します。
基板のたわみは、基板カットなどの工程で発生しますが、その場でたわみ量(曲げ深さ)を計測することは困難です。そこで、一般には、ひずみゲージを使用して、基板表面のひずみ量を測定します。
ひずみ量を測定して、値が大きくならないようにしてください。 - ・ひずみ量評価時の注意点
- (1) ひずみ量測定位置
コンデンサが実装された基板に、どの程度のひずみ量が加わっているかを測定する場合、ひずみ量の測定位置は、
コンデンサの横ではなく、コンデンサを取り外し、実装されていた位置で測定してください。
コンデンサの横では、コンデンサの剛性による影響を受けるため、基板に加わるたわみストレスの大きさを正確に
反映していません。また、評価基板の状態は、周辺の部材、はんだ及びはんだ量は、実際の実装基板に近い環境と
なるようにしてください。 - (2) 最大ひずみ量の発生方向
実際の工程で発生するひずみ量は、360°全方向で生じます。このため、ひずみ量は、3軸のひずみゲージを使用して
計測することを推奨します。ひずみゲージの取付け方向は、測定する位置に3軸のひずみゲージの中心軸を
合わせるように設定してください。
- (1) ひずみ量測定位置
ひずみ量について
- ・ひずみ量評価時の注意点
一般に金属は、外から力を加えて変形させると、電気抵抗が変わります。電気抵抗は断面積に反比例し、長さに比例します。この原理を利用すると、構造物に金属を接着して、その電気抵抗の変化を測定することで、ひずみ量が求められます。この原理を応用したのが、ひずみゲージです。
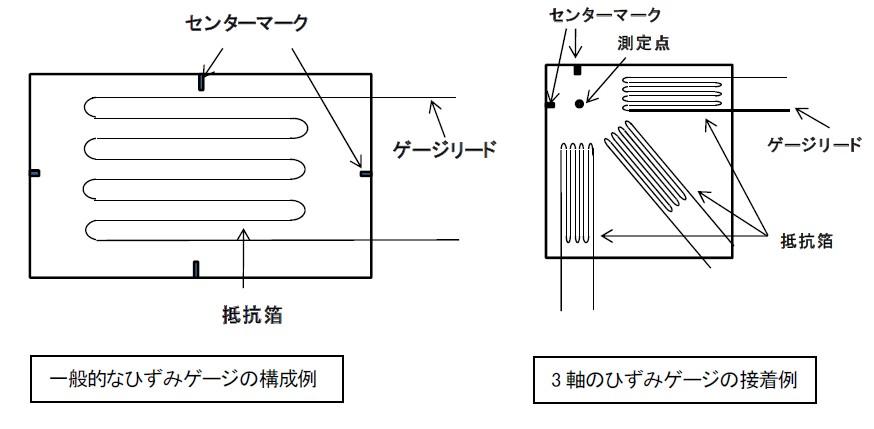
ひずみ量評価による改善例
各工程で、ひずみ量を測定したところ、基板カット時に、大きなひずみ量が発生することがわかりました。(ひずみゲージの接着例を下図に示します。)
この結果から、コンデンサ実装位置の近傍にスリットを設けました。この設計変更によって、基板カット時のひずみ量が低減し、コンデンサのクラックの発生を抑えることができました。
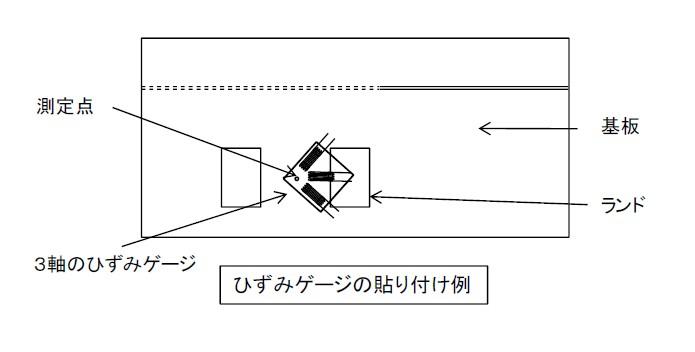
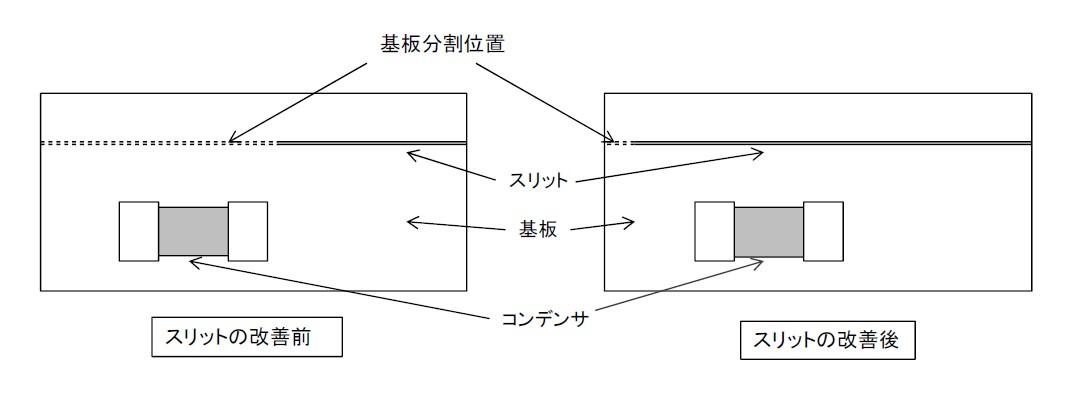